Technological Dynamics Under Valerism: From Catalytic Spectralization to Universal Modularization
A New Technological Vision for Future Societies
In my book, The Physics of Capitalism, I analyzed the internal technological dynamics of modern capitalism and explained how they were related to its external relations with the natural world. This post is an attempt to unveil what an entirely new cosmology of technological development would look like under valerism, the name I gave to a new framework for thinking about the relationship between nature and civilization. If capitalism is all about growth, valerism is all about stability, for global civilization and the biosphere as a whole. In effect, I’m presenting in this post an ambitious high-level vision for what technological development could look like in a post-capitalist society that prioritizes ecological sustainability.
There’s a lot of jargon in this post that I’ve defined and explained in prior posts and in the book. Before moving on, I would strongly recommend reading my very first post on Substack, as it will make understanding this post much easier. That post described the technological dynamics of conversional technologies under capitalism, and this post is a kind of companion post describing technological dynamics under valerism and how valerism would address the flaws and shortfalls of technological change under capitalism. For a short primer on valerism, I would recommend reading this post. Most of what's in this post is completely new work and builds on what I discussed in my book, which laid out a general vision for what the world could look like under valerism, but without taking a deep dive into one of the core issues: modularization.
Conceptual Introduction to Modularization
In the valerist order, the creation of a modular society, modularization, is one of the four great pillars, the other three being stabilization, socialization, and localization. In my book, I spent quite a bit of ink discussing stabilization and socialization, but I didn’t say enough about modularization and localization, and this post is an attempt to rectify that mistake. I will cover localization extensively in a future post. I emphasized in the book that these design principles are interdependent, meaning that we can’t pick and choose between them. If we want to create a global system based on stability and harmony with the broader biosphere, then we need to implement these principles jointly and simultaneously. Focusing on one but ignoring the other three would still lead to civilizational catastrophe. This is an important theme that will come up later in this post as well. Implementing aggregate modularization is extremely important, but not if it’s done without thinking about broader issues related to political economy, which the other pillars collectively address in a more direct and comprehensive way.
At a high level, modularization is the process of taking complex tasks or objects and breaking them down to smaller units that are more manageable. The classic toy example is a Lego set, where the same basic building blocks can be combined in an incredible number of ways to produce a wide array of different shapes and objects. The idea of modularization comes up often in many businesses processes, even for things like software, but the main focus of this post will be modularization as a design principle for the economic and industrial organization of consumer goods and conversional devices, which are physical systems that take energy from an input source and convert it to some other output. Examples of conversional systems would include smartphones, cars, refrigerators, and power plants.
Modularization can include interchangeable and reusable components for industrial manufacturing. It can include prefabricated modules for construction and housing. It can encompass interchangeable units for modular furniture and other consumer goods. The basic operating principles of a modular system are reusability, interchangeability, and prefabrication. To the extent that people pursue modularized strategies, they usually do so because of a desire to enhance efficiency and productivity. It’s also important to emphasize that modularization can encompass repeatable and automated tasks and processes, so it’s not just about physical items and their components. An object or a system can be modularized, but so can a manufacturing process.
These are the more familiar senses of the term, but the way I'm using it here is also a bit more expansive. First, modularization under valerism is meant to be universal and comprehensive, meaning that it’s supposed to cover all economic sectors and economic activities capable of being modularized, from extraction and manufacturing to transportation and products in end-use consumption. In other words, modularization is meant to be a macro-level design principle for organizing economic production, distribution, and consumption. Second, modularization under valerism is meant to change an economy’s internal dynamics of technological development, with the broader goal of more effectively constraining and regulating its energy scale, which is so important for limiting the extreme levels of waste and pollution that global civilization is currently dumping into the biosphere.
The goal of modularization under valerism is not merely to reduce waste and pollution or to recycle more materials, but to change the nature of technological development itself, as technological regimes are heavily implicated in the energy scales and efficiency dynamics of modern civilization. Third, valerist modularization is based on interoperability and integration. In a valerist framework, we shouldn't speak about modular systems so much as modular networks, technological environments where a broad range of conversional technologies are highly integrated. This way of using the term is a radical departure from previous work and emphasizes the harmonization of technological regimes by breaking down proprietary barriers and enhancing standardization. Fourth, valerist modularization places great importance on restricting the scope and scale of customization, which means creating relatively uniform product and technological standards.
A fundamental point I want to emphasize is that there are plenty of industries and sectors that are currently not modularized to the extent that existing technologies can achieve, largely because of political and financial constraints. In other words, the means and methods for modularizing these industries exist, but there are various political and economic forces that are working against the implementation of modular strategies. The most common barrier is simply high costs. Companies won’t undertake strategic modularization if they can’t afford it, which is why this shift simply cannot happen under the current capitalist framework. It’s the kind of major change that requires an entirely different kind of political economy, like the valerist system which I described in the book and which I have covered before in my other writings here on Substack.
Finally, let me mention how modularization differs from automation. The two concepts obviously overlap to a significant degree, as they are both often used to minimize human intervention in technological processes. But not all acts of automation need to be done through modularization, and not all acts of modularization necessarily lead to automation. It’s possible to modularize a particular system or process and still require a fair degree of human intervention, whereas the goal of automation is more specifically directed at removing the necessity for human action. As a design philosophy, modularization is also meant to highlight how the different parts and components of a system align and work together, in the hope of making the system more robust, resilient, and adaptable.
Concrete Examples of Modularization in Different Industries
Before going any further, it’s useful to have some concrete examples of modularization in mind. In this section, I’ll review a mishmash of historical examples, established technologies, and proposed initiatives across various industries, to see how modularization has played out in concrete reality at large scales of industrial production and end-use consumption. I will actually refer to some of these examples throughout the post as I’m making broader arguments.
Let’s begin with WindSpider, a Norwegian company that is trying to scale a clever self-assembly platform which uses an automated crane to lift the necessary components for building wind towers and turbines (see Figure 1). The company’s technology holds the promise of making offshore wind power construction much easier, but it’s still too soon to know what the ultimate impact on the industry will be. Nevertheless, it’s a compelling example of a groundbreaking modular manufacturing process, underscoring that modularizing repeatable tasks and processes should be a key initiative for the rapid deployment of renewable energy systems.
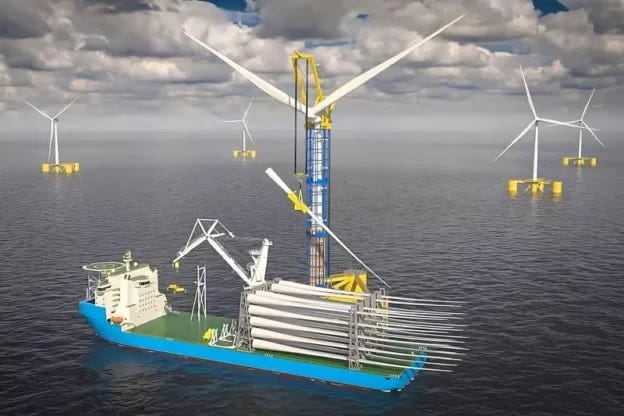
Modularized production in the auto industry is increasingly common and has been around for a long time by now. The hallmark example is probably Volkswagen’s MQB system, a modularized chassis that provides a common platform for building a wide range of vehicles, from hatchbacks to SUVs (see Figure 2). Volkswagen Group automakers have produced millions of cars with this platform, which has boosted production efficiencies and facilitated faster development cycles. The platform features a transverse engine design and other prefabricated components that collectively form a standard base on which to build a full car. The platform has enough flexibility that it can even accommodate multiple powertrain options and designs, from gas-powered vehicles to EVs.
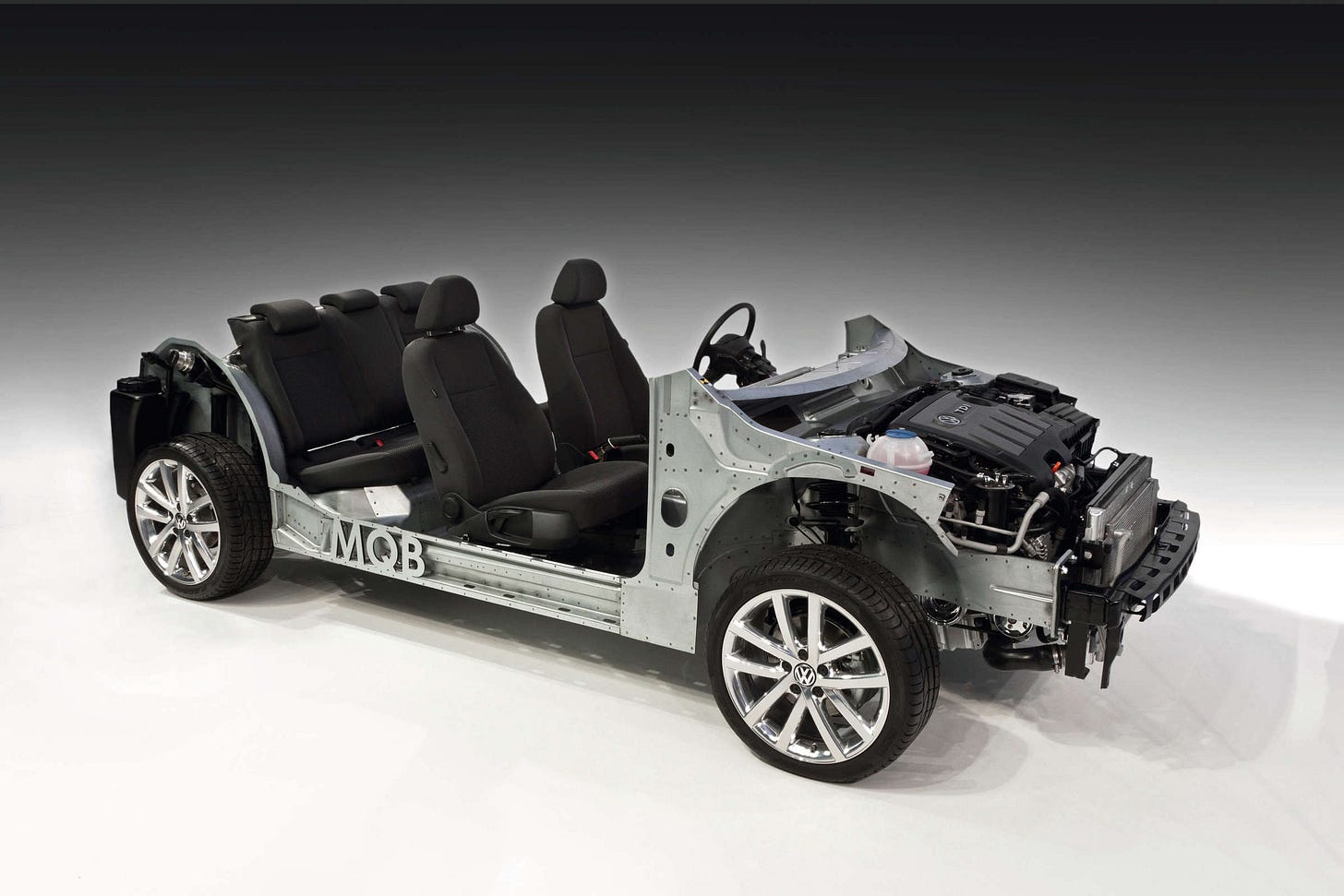
The Nakagin Capsule Tower in Tokyo was a mixed-use building that contained offices and apartments during its operational phase (see Figure 3). Its striking features made it instantly recognizable. The building was eventually demolished and some of its capsules were repurposed for other uses. But it highlights the creative potential of modular construction, which has become increasingly popular in many places around the world. Modular housing, in particular, is often stereotyped as ugly and undesirable, but there’s no reason why we can’t achieve architectural ingenuity with modularized designs.
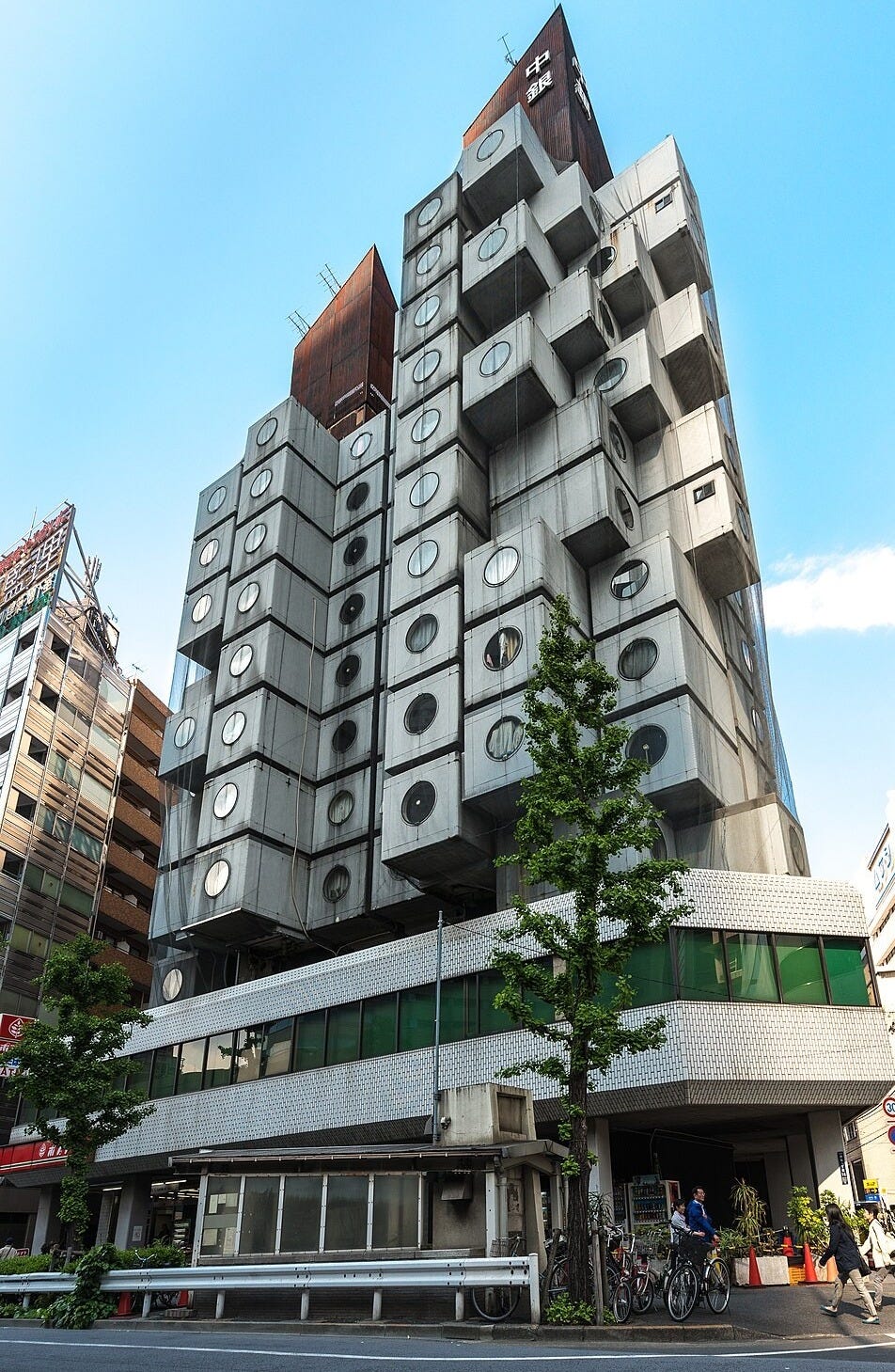
The Theory and Evidence on Modularization and Resource Consumption
In my book, I argued that, from a biophysical perspective, economic systems are best understood as conversional networks, meaning they consist of conversional devices, like smartphones and power plants, that consume energy from some source and convert that energy into useful tasks, from the transportation of vehicles to the production of consumer goods. These conversional devices are embedded in complex networks with dynamic feedback loops, and this interdependence ensures that changes to one part of the network reverberate to other parts of the network. When a change is made to a conversional device that affects the efficiency or power output of the device, I call that a spectralization. Some conversional spectralizations are so intense and catalytic that they diffuse widely and cause many upstream and downstream changes across the conversional networks of an economy, expanding its aggregate energy scale. Steam engines and AI chips are two major examples. This is the regime of catalytic spectralization that characterizes technological change in modern capitalism, and it’s so wasteful and energy-intensive that it’s putting the entire health and stability of the planetary biosphere in jeopardy. Universal modularization is the valerist answer to catalytic spectralization under capitalism, so let’s try to better understand how it works and why. A good place is to begin is by reviewing some of the empirical evidence on the benefits of modularization.
In a major study from 2012, Lu Aye and his collaborators demonstrated the ecological benefits of modular construction by analyzing an eight-story multi-residential building. They found that steel-structured prefabricated systems reduced material consumption by up to 78% by mass in comparison to conventional concrete construction methods. A study from South Korea found that modularized construction techniques produced 36% lower embodied carbon emissions relative to the traditional reinforced concrete process. The automotive sector is also increasingly relying on modular production platforms. In particular, the rise of Modular Electric Vehicle Platforms (MEVPs) is creating more efficient production cycles compared to traditional alternatives.
A 2016 review of the performance of modular buildings, including their energy performance, found that they did better than competing alternatives. The authors of this study noted that, in 1998, over 75% of all new annual homes in the United States were built on-site. The authors described modular buildings as follows:
Modular buildings are a set of modules that are built in an off-site fabrication center, delivered to the construction site, assembled, and placed on the permanent foundation. A modular building normally has multi-rooms consisting of three-dimensional modules. The modules are built and preassembled in factory environments…Upon completion by the manufacturer, these units are shipped to the site for installation on foundations much like a site-built project. About 85–90% of the modular construction is done off the construction site and the remaining work (10–15%), including foundations and utility hookups, is done on site. The application of modular construction is found mainly in general building construction, particularly apartment buildings, schools, hotels, student housing, hospitals, offices, single-family developments, correctional facilities, floating projects, and other buildings where units are repetitive.
Many studies have examined the energy use and emissions associated with specific modular buildings and constructions. For example, a 2018 study of a prefabricated building module in Sicily found that it had relatively low levels of carbon emissions and primary energy consumption, achieving a Net Zero Energy Building rating, defined as a building that consumes as much or less energy as a renewable source powering the building. Even modular steel bridges have been shown to have a much lower environmental impact compared to their concrete counterparts.
In a 1997 study, Rogers and Bottaci proposed creating "modular production systems" for manufacturing in the space of low-end and mid-range consumer goods, like toys and kitchen appliances. In manufacturing, principal assembly is the traditional method of production, where goods and components are processed through a fixed sequence of steps, kind of like an assembly line, that eventually culminates in a finished product. By contrast, modular assembly is a more flexible and adaptable strategy that focuses on building modules in off-site locations and the putting them all together at a dedicated facility. The authors propose creating four modules for their modular production systems: process machine primitives (physical machines doing the work), modular actuator elements (motion tasks), modular tooling (hardware to facilitate integration of primitives and actuator elements), and configurable control systems (communication network to make sure the modular systems are working well together). From this fundamental set of modules, they call for two new manufacturing principles: just-in-place parts production, focusing more on the production of components rather than final assembly, and automated production system design, for creating tools to model and perfect manufacturing processes. This is a model that won’t necessarily be effective everywhere, but holds immense potential across a wide range of industries, as it can significantly boost production efficiencies.
The implementation of common technological standards is important if we want to ensure interoperability and interchangeability, and thus directly implicates the importance of political economy in pursuing effective modularizations strategies. The adoption of the USB-C standard by the European Union is a canonical recent example, and soon enough all electronic devices sold in Europe will be required to use the same charging port. This policy shift in Europe finally forced Apple to drop its Lightning connector and to transition to USB-C starting with the iPhone 15. Now you'll be able to use one cable to charge everything, instead of keeping track of separate charging components for Apple and Samsung products.
Dominant corporations prefer proprietary products they can defend through patent litigation, to better ensure market exclusivity but also to hijack their customer base by making it difficult to switch to other products, supplemented by planned obsolescence that forces those locked-in customers to keep buying often. The main goal is to erect technological fiefdoms, which then encourages greater spectralization as hyper-specific conversional systems and technological standards proliferate within these feudal domains. Not all of these spectralizations will become mega-catalytic like steam engines or AI chips nowadays, but many of them will definitely put upward pressure on resource and energy consumption. The 1956 consent decree between AT&T and the US Department of Justice is probably the landmark example of government intervention in establishing technological standards. The agreement forced AT&T to license its patents for a reasonable royalty to any company that requested them, while also requiring AT&T to exit from general electronics and to just focus on phone-related technology. The subsequent diffusion of transistors led to the miniaturization of computers and paved the way for the era of personal computers, forever changing the world. Combined with the 1968 Carterfone decision that allowed external devices to electrically connect to the AT&T network, these regulatory changes collectively promoted interoperability among a wide range of networks and devices.
The kind of universal modularization that I’m advocating would make the spectralization of conversional technologies much more difficult. It would simply be impossible or impractical for a company to introduce major changes to conversional methods if those methods cannot be properly integrated into existing modular networks, which, while they would allow for technological variations, would only do so under tighter conditions. Consider Volkswagen’s MQB platform again. Because it’s designed to handle transverse engines, another car company can’t just come along and say they want to start using in-line engines all of a sudden. Of course, they could in principle, but then they’d have to redesign and overhaul much of their production process, and the costs of doing that would be so prohibitive that most companies wouldn’t even bother. This applies not just to companies that are owned by the Volkswagen Group, like Audi and Bentley, but also to other companies that have a strategic partnership with Volkswagen. For example, Ford has agreed to use the MQB platform for manufacturing the Tourneo Connect, which is produced by Volkswagen in Poland. And all of this leaves out potential intervention from the state, through legal mandates on new technological standards, nationalizations of existing industries and companies, enhanced regulatory frameworks, or combinations of all these things.
Modularization in Housing and Renewable Energy
Housing is a hallmark example of an economic sector that can be thoroughly and comprehensively modularized, provided the political will exists to make it happen. In the United States, modularization in the housing industry has never really taken off. Research has shown that less than 4% of the US housing stock was built using modular methods, in contrast to about 15% of homes in Japan and 45% of homes in many Scandinavian countries. As far as modularization goes, the United States housing market faces intense headwinds from a patchwork of local building codes, local architectural styles, consumer design aesthetics, and financing constraints from private banks, many of which would be unwilling to fund modular housing developments. As I’ve argued in an earlier post on housing, fixing these and other related issues would require overhauling our political economy, and I’ll bring up one of the primary examples from that post again.
When communist governments came to power after the Soviet victory in World War II, they launched a large-scale building campaign to provide housing for their devastated countries, using pre-fabricated housing components to construct things cheaply and quickly. The modularization of this housing boom created massive efficiency and productivity gains, allowing governments to build millions of units in a rapid amount of time. That historic push led to a wave of new apartment towers and city blocks, providing mass public housing to millions of people. The apartment blocks have often been stereotyped as ugly and unappealing in the West, reflecting the bourgeois sensibilities of those making the criticism. But for hundreds of millions of people, they were and continue to be a vital lifeline for cheap and stable housing, automatically eliminating one of the great stresses of life. And the market for these communist-era apartment homes remains quite strong. The Czech Republic is a great example, as the panelák building complexes from communist times still housed, as of 2005, roughly one-third of all Czechs, an astonishing 3.5 million people (see Figure 4).
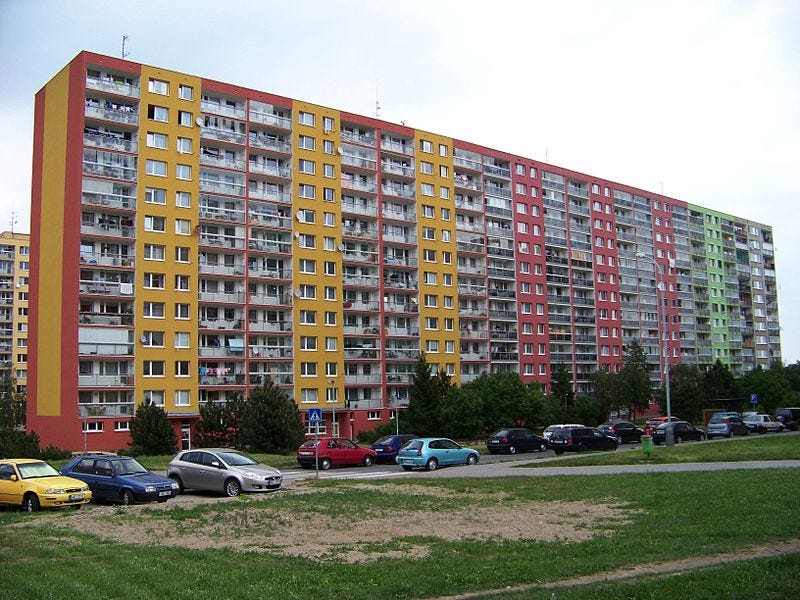
Restricting customization through modular manufacturing and modular design strategies led to phenomenal economies of scale, allowing entire mini-cities to go up in months or a couple of years, a breakneck pace unheard of in much of the Western world, where the obsession with luxury aesthetics and customized designs often overrides practical issues around functionality and affordability. We need a total revolution in the meaning of housing, with the adoption of modularized design and manufacturing strategies that can produce rapid economies of scale and deliver major results in a short period of time. That means prioritizing things like functionality, affordability, and walkability over aesthetics and luxurious amenities.
Modularization in the renewable energy industry has typically taken the form of prefabricated components that are transported and installed on-site. Modularization is common for things like solar panels, wind turbines, and especially battery storage systems, which have made enormous gains and strides in the United States over the past few years (see Figure 5). The rise of modularized container designs contributed heavily to this expansion because it made these systems extremely scalable, another hallmark example of the sheer power of modularization to allow for the rapid deployment of products and resources in just about any given market. Of course, there’s no doubt that regulatory changes and additional financial support from the federal government spurred a lot of investments into battery storage systems, but modularization was a critical reason why all this new supply was activated so quickly.
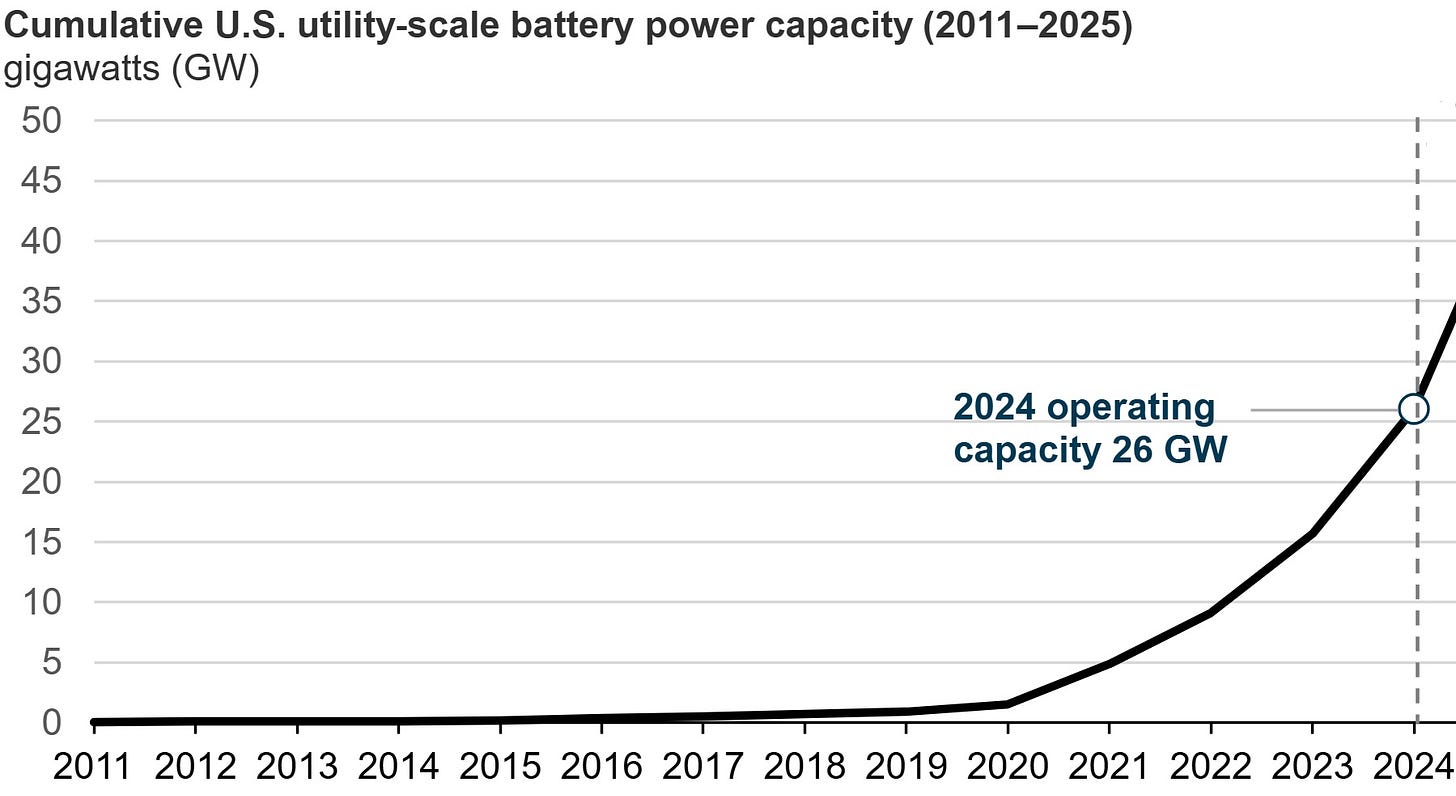
Modularization, Planned Obsolescence, and Consumer Goods
Capitalists are very skilled at blabbering about efficiency and innovation as they push for financial accumulation and expand the underlying scale of their energy systems. In 1924, the world’s major light bulb companies formed a secret cartel called Phoebus, after the Greek god of light. The main purpose of the cartel was to mandate new manufacturing standards that would reduce the planned lifetime of an incandescent light bulb. By the early 1920s, rapid technological development had significantly improved the lifetime of the average light bulb, to the point where many of them could last as long as 2,500 hours. But that turned out to be a problem for the light bulb companies: better-lasting bulbs were hurting sales because consumers could wait a much longer time before buying replacements. To remedy the problem, the companies of the cartel ordered their engineers and manufacturers to produce light bulbs that would only last 1,000 hours. Their public justification for this move was an apparent desire to improve efficiency, but recently discovered internal documents from some of the companies make it apparent that the real reason for the shift was to boost sales.
The formation of the Phoebus cartel has sometimes been called the birth of planned obsolescence, which is the process of designing and manufacturing products to ensure their rapid breakdown, thus bringing consumers back to purchase additional versions of those defective products. Planned obsolescence is, in effect, a form of technological sabotage disguised as an apparent innovation. It has become a cornerstone of corporate planning under capitalism, impacting everything from personal vehicles to electronics. For example, Apple used to slow down older iPhones to encourage customers to buy newer variants. And when iPhones broke down, Apple made it very difficult to access certain critical components that had to be replaced, as a way of ensuring, once again, that customers ended up buying an entirely new phone instead of just replacing the defective component in question. Apple is also notorious for engineering a highly closed ecosystem of devices and technologies to ensure customer lock-in. Many companies play these kinds of games. Because high-tech commodities are designed to fail quickly, they must be continuously reproduced, repackaged, and reshipped so they can be sold to consumers. That process requires large amounts of energy. One of the biggest effects of planned obsolescence is to therefore reinforce the energy-intensive nature of capitalist production and distribution.
Universal modularization would end planned obsolescence by promoting greater reusability, interchangeability, and interoperability. If a component breaks down, we don’t need to throw away the entire system. We can simply replace the modularized component. This principle would extend across all economic sectors, even for things like consumer goods, which are frequently thrown away or entirely replaced when one of their components has a defect.
Consumer goods are a major area of future growth for modularization. There are many consumer goods that are already modularized, including furniture, but there are plenty of other consumer categories that could still benefit from it (see Figure 6). And even in areas where modularization is present, it’s not necessarily widespread. Many furniture pieces remain highly customized and specialized, making them difficult to repair or sustain over the long run. The success of modularization is therefore critically dependent on restricting the scope and scale of customization. If we modularize 50,000 different types of tables, the very process of scaling the manufacturing for these tables would backfire and lead to skyrocketing energy use. But if we modularize 200 different types, it’ll be much easier to master the production process for each one, to produce large numbers of spare components to high levels of quality, and to limit energy use and resource consumption from this sector. Enacting this project would require imposing common standards on consumer goods and sacrificing some desired aesthetics (see Figure 4).
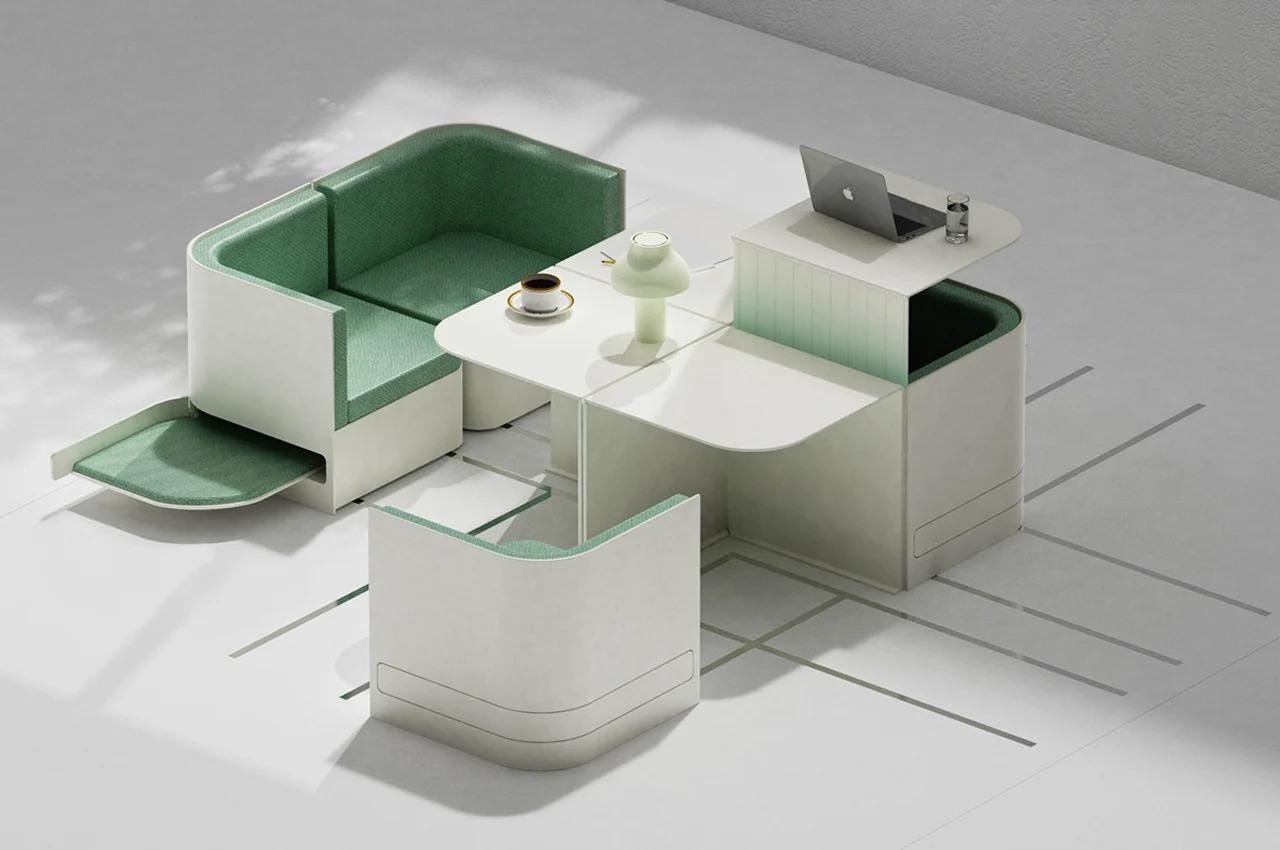
Modularization can only be successful for our long-run energy and ecological goals assuming that it's paired up with restrictive customization. This goes back to the concept of a modular network: modularizing housing would also make it easier to modularize common things that go in most homes, like furniture, as well as appliances. The point is that when we think about what modularization could look like in a different kind of economy, we shouldn’t just be focusing on modularizing specific items, we should be modularizing entire conversional networks and technological ecosystems.
Modularization in Robotics
The recent public obsession around AI has been all about the generative AI wave epitomized by systems like ChatGPT, Copilot, and Grok. In the corporate world, there's now a major push towards agentic AI, autonomous systems that are supposed to help workers with everything from writing code to responding to customer questions. But in a very real sense, this is all low-hanging fruit. The ultimate AI dream is all about robotics, from humanoid robots that can function like human beings in a three-dimensional world to industrial robots that can automate and accelerate production. Robotics is the final frontier of AI. Robots are already all over the place. There are millions of them in factories worldwide. As of 2023, there were almost 2 million industrial robots in Chinese factories alone. When the global population plateaus and starts declining later in this century, robots will be necessary to perform vital tasks that human beings just won’t be available to do.
Modularization in robotics can encompass many different systems and processes, but I want to begin in a part of the industry that already has practical solutions in place but is struggling with scalability: warehouse automation. Modularizing warehouses also offers a great example to study the possibility of robotic modular networks and what they might look like in practice. Enhancing interoperability and interchangeability in this environment would require modularizing and integrating trucks, docking stations, pallets, robotic arms, mobile robots, and warehouse layouts, among other features and components. The goal is to modularize the network as a whole, not to focus on individual units while ignoring the broader picture.
Let's consider Symbotic, a major robotics company that operates AI-powered mobile robots for warehouse automation. On paper, its systems are highly modularized and offer flexibility and rapid scalability in different environments (see Figure 7). Symbotic robots are built from modules and feature many interchangeable components. And the entire Symbotic warehouse system is robust against individual points of failure. If some robots break down, others will continue operating, the kind of system-level resilience that’s a key benefit of modularization. But despite this level of modularization for its robotic fleet, Symbotic has struggled to deploy more than a few new warehouse systems per year in its recent history.

Symbotic robots are complex machines, and although they're designed with modular principles in mind, the company has outsourced part of its manufacturing to external contractors, so it can take a significant amount of time to produce a fleet of robots for a new warehouse deployment. Beyond that, every warehouse environment is a little bit different, so it might take a lot more effort to implement the automation system in one warehouse versus another. Even though Symbotic may have modularized the underlying components of its robots, the broader technological ecosystem in which those robots are operating has not been modularized, and therefore presents major challenges when it comes to rapid deployment and scalability.
Whether in robotics or any other industry, we need to be mindful about safety when implementing modularization. Sometimes it’s possible to modularize a system or a process but lose certain safety features along the way, and a great example is with autonomous driving. Waymo uses a more advanced suite of sensors than Tesla’s FSD. For example, Waymo uses LiDAR, radars, and a whole array of advanced sensors, in addition to a pre-mapped three-dimensional environment that gives the car a better sense of where it is and what it’s doing. By contrast, Tesla’s FSD uses an array of cameras and an AI-enhanced system to figure out where it’s going. Tesla’s system has the advantage of being more scalable and can operate in a broader range of environments. Waymo typically operates in more limited environments, but delivers a strong safety record in those environments, whereas Tesla has often been accused of major safety lapses, though it’s difficult to get an accurate picture of its actual safety record. Nevertheless, with autonomous driving or other areas in robotics, we’re going to learn through experience and trial-and-error where to strike the balance between the need to modularize and the need to maintain proper standards of safety and quality control.
There are many opportunities for further modularization in the robotics industry. Highly modularized systems like swarm robots are increasingly being used for construction, manufacturing, search and rescue, and exploration of challenging environments. Force-torque sensors are great candidates for further modularization across a range of robots, to a greater extent than what’s been currently achieved. In general, there are opportunities to modularize many kinds of actuators (the devices that provide motive force for the robot, like electric motors) as well as end-effectors (the devices that perform a specific task, like grippers). A major area of opportunity for enhanced modularization is in robotic charging stations. Just like phone chargers were once customized and hyper-specialized across proprietary domains, many companies in the robotics industry haven’t integrated their charging systems and ports. This is an easy place for government intervention to help set those common standards and ensure all robots are basically charged using the same set of processes, methods, and ports. But there will be limits to where modularization can take robotics. Some tasks and processes are so specific and hyper-specialized that modularizing them to a significant degree would be impractical. Electroactive polymers, increasingly being used as actuators in prosthetic limbs, are a great example, as they can be difficult to control and there’s a lack of uniform standards for ensuring their integration with other robotic systems. Like with everything else, figuring out what works in the best way is a matter of give-and-take and trial-and-error.
If it all goes according to plan, the robotics industry could automate much of its own manufacturing, turning everything into a self-organized recursive process. One day we could have robots building other robots, robots repairing each other, and robots forming an integrated technological ecosystem. Human intervention would become largely formal and perfunctory in this modular meganetwork.
Conclusion: Modularization in the Larger Valerist Order
Universal modularization is not a panacea. To be effective at achieving the broader goals of valerism at a global level, modularization must be accompanied by radical changes to global political economy. If that doesn’t happen, modularization will become just another empty slogan commandeered by corrupt capitalists who want to give the outward appearance of caring about ecological sustainability while doing practically nothing to actually achieve it.
For example, if we pursue modularization but don’t change the nature of international trade by insisting on localization, then what’s going to happen is that major corporations will prefabricate components in countries with cheap labor and ship those components halfway around the world so they can get to their final destination. Indeed, this is already happening in many industries, like fashion, but it would just happen at a far bigger scale if different countries imposed universal modularization on their economic systems but didn’t reform the broader contours of global trade and the supply chains that come with it.
Next, let’s consider how modularization would mix with socialization, or the transition from private ownership to public ownership. Sure, a government can always impose rigorous technological and product standards on manufacturers and consumers and while enforcing those standards through a tight regulatory regime. In plenty of cases, this kind of approach will work just fine. But in many other cases, especially energy-intensive industries with highly extended supply chains, where it’s not so easy to monitor the production and distribution of modular components, it actually makes far more sense to build internal state capacity and resort to nationalization, providing direct state ownership over the means of production. I explored arguments for socialization at a deeper level in the book itself, but the basic point I’m highlighting here is that modularization would often be easier to implement at larger scales if the state had more direct levers of control over production and distribution.
Finally, I want to address the relationship between modularization and the Jevons Paradox. I covered the latter extensively in my book and in my first post on Substack. Since modularization would lead to massive efficiency gains and rapid scalability, we need to be careful to make sure that it doesn’t backfire. Efficiency gains in the history of capitalism are often major drivers of more energy use and resource consumption. That’s where stabilization, the first pillar of valerism, comes in. In the book, I call for implementing caps on annual average daily per capita energy use, and I clarified that a valerist society should stick to something between 30,000 kilocalories and 60,000 kilocalories. Most industrialized economies are currently outside of this range, though some are very close to the upper bound while others are very far from it. Imposing these kinds of energy and resource constraints, as a fundamental goal of our political economy, would prevent the worst excesses of any modular strategies. As I’ve said all along, the goal isn’t for modularization to change the world all by itself. It simply cannot do that. The broader goal in valerism is to create a modular society that operates under the direction of a new kind of political economy, one that prioritizes the needs of the working class while also ensuring the stability and habitability of the planetary biosphere.
I very much appreciate your thinking and expertise.
Great article. But these are not new arguments: in the late 1800s August Bebel and other early-day Social Democrats argued that capitalism incorporates planned obsolescence to up sales, argued for modularisation, and also argued that society should be organised around use-value and not exchange-value. (I just happen to be reading Bebel’s biography . . . .)